Have you ever wondered what goes into making those fluffy, warm-down comforters that you love to snuggle under? As it turns out, creating high-quality down comforters is an intricate process requiring special materials, advanced equipment, and artisanal techniques passed down through generations.
In this beginner’s guide, we’ll give you an inside look into how down comforters are made, from the sourcing of the down and feathers to the final stitching of the cover. You’ll learn all about:
- The different types of down clusters and feathers used
- Industry standards for ensuring responsible and humane down sourcing
- Steps in the manufacturing process like cleaning, treatment, and down-proof sewing
- Key materials like downproof fabrics and thread
- The importance of high-precision sewing machines
- Handcrafted details that set artisanal brands apart
- Care and maintenance best practices
Whether you’re in the market for a new down comforter or just curious about how they’re constructed, read on for an in-depth look at the making of this bedding staple.
Down vs. Feathers: What’s the Difference?
The first step in understanding how down comforters are made is recognizing the differences between down and feathers:
- Down: The undercoating of waterfowl consists of light, fluffy filaments that grow along the body to provide warmth and act as a natural insulator. Down clusters trap air between filaments to retain heat.
- Feathers: The exterior covering of birds consisting of a central shaft with branches called barbs extending out from either side. Feathers are more structured and rigid compared to soft-down clusters.
The highest quality down comforters use a higher percentage of down clusters, typically from geese or ducks, to provide unmatched coziness and heat retention you can snuggle right into. Lower grades may contain more feathers which reduces overall softness and insulation capability.
Now let’s look at how manufacturers source and prepare the precious down and feather raw materials.
Ethical Sourcing: Ensuring Humane Practices
Reputable suppliers follow strict protocols to ensure animal welfare from hatching to processing. Two leading organizations include:
- Responsible Down Standard (RDS): A global standard for humane treatment of geese and ducks with certification for each stage of production from farm to processing facility.
- The International Down and Feather Testing Laboratory (IDFL): Provides testing along with the International Down Pass certifying fill materials are ethically sourced from ducks and geese.
By sourcing fill materials from certified vendors following RDS and IDFL protocols, brands can ensure responsible, ethical treatment of fowl at all times. Some top brands and retailers known for responsible down include Cuddledown and Plumeria Bay®.
The Down Comforter Manufacturing Process
Producing a high quality down comforter is a detailed, multi-step process. Let’s break it down.
Step 1: Down Cleaning and Sanitization
Freshly harvested feathers and down contain natural oils, dirt, and debris that must be thoroughly cleaned before use in bedding. Responsible manufacturers use advanced sanitization techniques to produce ultra-clean hypoallergenic filling free of impurities:
- Multi-wash cycles to eliminate dirt, fungi, and bacteria
- Dry-steam sterilization using extremely high temperatures to sanitize down
- UV ray disinfection to eradicate microorganisms without using water or detergent
This comprehensive cleaning leaves fill material medically clean and safe for those with allergies or sensitivities.
Step 2: Drying and Conditioning
After intensive washing, specialized dryers remove all residual moisture from freshly cleaned downs to prepare the fill for comforters. Conditioners may be added to increase loft, resilience, and longevity of the delicate filaments.
This careful processing ensures long-lasting performance and prevents bacterial growth once inserted into the finished bedding product.
Step 3: Baffle Box Construction
Baffle box construction is the hallmark of quality down comforters. This technique utilizes down proof fabrics with a very high thread count and specialized sewing to create fabric walls dividing the comforter into separate chambers:
- High thread count fabrics like sateen prevent fill from poking through
- Narrow fabric walls create baffle boxes to hold fill in place
- Small stitches securely join fabric without holes for leakage
Thanks to these meticulously sewn baffles, the lightweight fill stays evenly distributed without shifting or clumping in your comforter.
Constructing baffle boxes requires special sewing machinery and handiwork for quality construction:
- High precision programmable sewing machines capable of consistently making tiny, close stitches
- Advanced optical sensors to ensure perfectly straight seams
- Special tables to support the fabrics during sewing
- Skilled sewing machine operators to handle the multi-step production process
This proprietary machinery along with seasoned artisans allow factories to expertly craft durable baffle boxes preventing leakage over years of use.
Step 4: Filling Each Baffle Chamber
Once sewing is complete, it’s time to carefully fill each baffle box with sanitized down and feathers. Most often, this process is done by hand to gently fluff and distribute fill evenly throughout the chambers.
Measuring equipment weighs out exact amounts before workers gently tamp each area to remove air pockets and prevent clumping or gaps in insulation. It’s meticulous work requiring time, skill, and care to guarantee even distribution for consistent warmth.
Step 5: Final Sewing of Shell
The last stage entails enclosing the filled comforter within a decorative outer shell made from fabrics like cotton sateen or Egyptian cotton.
Workers expertly feed the top and bottom layers through specialized sewing machines to enclose fill and join both sides together. The final stitch pattern depends on the style and manufacturer preferences:
- Sew-through box stitch: Straight stitches joining the top and bottom in a grid pattern
- Diamond quilting: Fancy diamond shaped stitch work creating depth and texture
- Channel quilting: Lengthwise lines allowing maximum height and loft
Whatever pattern is chosen, this last quality inspection ensures the outer fabric and inner baffles are securely fastened together into a durable down-filled bedding masterpiece!
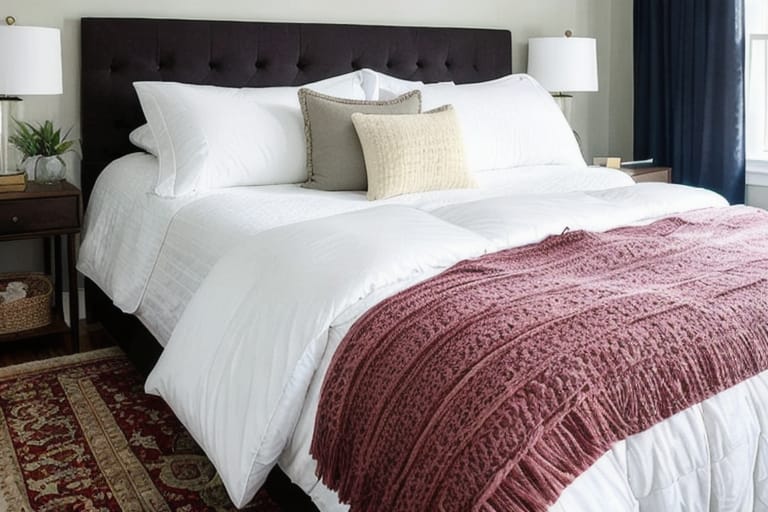
What Makes a Down Comforter “Down Proof”?
As described above, down proof fabrics with densely woven threads are vital to keep insulation neatly tucked inside over years of use. But what exactly makes a fabric down proof?
- High thread count – Typically over 300 threads per square inch
- Tightly woven – Yarn and stitches packed closely together
- Specialty textiles – Ultrafine microfibers or dense canvas cloths
With these properties, no feathers can poke through even after repeated wash cycles. Compared to traditional cotton shell fabrics more prone to leakage over time, high quality down proof textiles retain loft and prevent fill from shifting around.
Spotlight on Artisanal Down Comforter Brands
While most bedding brands import down to construct comforters, several exceptional companies based in the USA differentiate with handcrafted construction for unparalleled quality.
Let’s look at two standout artisanal players committed to domestic manufacturing using responsible regional sourcing and materials.
Cuddledown – Family-Owned Since 1972
Established in 1972 and still family owned, Cuddledown is a renowned manufacturer of premium bed and bath products made by hand in their Fall River, Massachusetts factory.
Their down comforters earn accolades for outstanding craftsmanship featuring:
- Hungarian White Goose Down sourced from Canada
- 600+ fill power for superior loft and lightweight warmth
- Durable German-imported microfiber shell
- Baffle boxes with double needle stitching and corner ties to prevent shifting
- OEKO-TEX certified hypoallergenic fill and fabric
As longtime domestic producers with heritage craft techniques, Cuddledown offers customization options for made-to-order bedding backed by stellar service and support. Their white goose down comforters deliver cozy luxury fully customizable to each sleeper’s preferences.
Plumeria Bay® and Cascade MadeTM – Pacific Northwest Pair
This dynamic duo based in the Pacific Northwest consists of down supplier Plumeria Bay® providing fill materials to bedding producer Cascade MadeTM crafting the finished comforters by hand in their Seattle factory.
Sourcing expansive fill exclusively from Canada to meet RDS standards, Plumeria Bay’s ultra-clean down passes stringent third-party auditing for ethical treatment. This exceptional down gets transferred next door for insertion into Cascade Made’s quality sewn comforters punctuated with:
- 600+ fill power feathers and down
- 300 thread count, 100% cotton sateen shell
- Double-needle sew through construction
- IDFL certified for responsible sourcing
Sold direct-to-consumer online, this joint operation controls everything from sourcing to production to sales, creating the ultimate farm-to-bed comforters made locally in the Pacific Northwest.
Down Comforter Care Tips
Caring properly for your down comforter ensures it stays clean, fluffy, and warm for the long haul. Here are top care and maintenance tips:
- Dry clean only – Use a reputable dry cleaner to launder or check if the manufacturer offers cleaning services
- Gentle cycles – Low heat delicate settings if machine washing; air or low heat tumble dry
- Tennis balls – Adding a couple of tennis balls helps break up clumps
- Spot clean – Use a professional spot remover for stains instead of dunking the whole comforter
- Air out – During storage or before bed, give your comforter a fluff by hanging to air out
- Re-cover – To give your comforter a new life, ask brands about re-covering services to replace outer shell fabrics
With proper care for the quality fill materials and outer shell fabrics, a high grade down comforter can realistically last over a decade.
Down vs. Down-Alternative Comforters
For shoppers with allergies concerned about responsibly sourced goose or duck down, down-alternative comforters offer a compelling option:
- Hypoallergenic synthetic fibers mimic down properties like softness, loft, and warmth without allergens
- Pesco or PrimaLoft® fills made from recycled plastic bottles or sustainably sourced minerals
- Affordable compared to premium down ranging from $50-$300
- Easy care suited for frequent machine washing and drying
The main tradeoff is that synthetic versions tend to be heavier and less breathable than natural down. But for allergy sufferers, ethical vegans, or budget buyers, quality down-alternative bedding delivers solid performance.
Glossary of Down Comforter Terms
Want to learn more about materials and manufacturing processes? Check out this glossary explaining essential terminologies.
Down and Feathers
- Down clusters: Fluffy assemble of soft undercoating filaments from waterfowl that provide insulation
- Plumules: A single piece of down comprised of delicate filaments branching from a central point
- Feathers: Exterior rigid structures covering birds consisting of a central shaft with barbs extending on both sides
- Fill power: Industry rating from 300-900+ indicating fluffiness and insulation warmth of down products
- Staple: Individual filament length impacting down quality and fill power
Fabrics
- Down proof: Tightly woven fabric using fine threads and special construction to contain feathers inside without leakage
- Thread count: Number of horizontal and vertical threads per square inch of fabric
- Sateen: Durable cotton fabric with lustrous sheen, often used for down proof outer shell
- Baffle: Separate fabric compartments sewn to subdivide and contain insulation fill
Manufacturing
- Baffle box: Box stitch comforter construction featuring fabric walls dividing fill into separate chambers
- Sew-through: Joining top and bottom comforter fabrics with lengthwise stitch lines allowing insulation height
- Diamond quilting: Decorative diamond pattern stitching that pulls top and bottom together
- Channel quilting: Straight line stitching allowing maximum insulation height without compression or shifting
The Thread Count Myth
If you’ve shopped for bedding before, odds are you’ve heard statements like “the higher the thread count the better!” But is this true when it comes to down comforters? Not quite.
While thread count indicates fabric density, there comes a point of diminishing returns. In practice:
- Once you hit around 300-500 thread count with high quality fibers like long staple Egyptian or Pima cotton, improved durability is marginal beyond this point.
- Ultra-high 1,000+ counts tend to use low quality short fibers that compromise longevity despite impressively high numbers.
More important indicators of durability for down proof fabrics include:
- Yarn quality – Long staple yarns last longer vs. short loose fibers
- Weave tightness – Are stitches packed closely together?
- Chemical finishes – Harsh acids and additives can weaken fabrics over time
So a comforter with 350 thread count tightly woven 100% Egyptian cotton will likely outlast a cheap 1,200 thread count product prone to tearing. As the adage says, don’t judge a book by its cover!
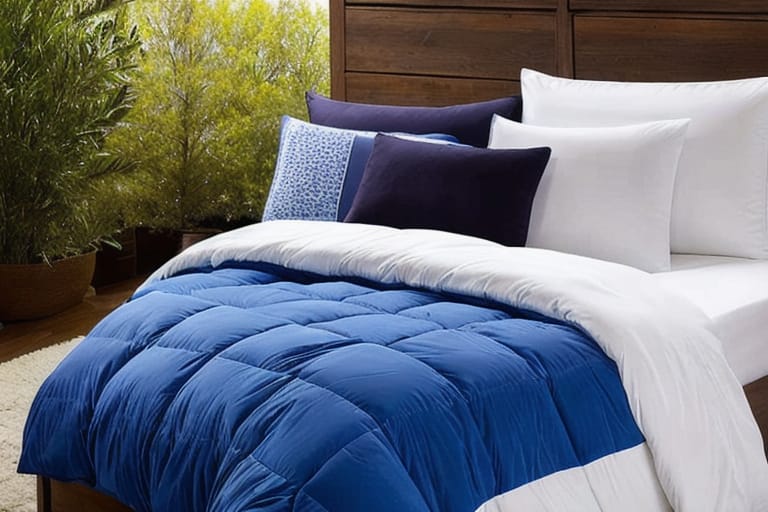
5 Takeaways
To wrap up this down comforter-making crash course, let’s recap major points:
- Responsible sourcing following ethical protocols ensures humane treatment of fowl that supply insulating down and feathers.
- Multi-stage cleaning utilizes technologies like UV sanitization to remove impurities for hypoallergenic fill free of bacteria.
- Baffle boxes created by specialty sewing systems securely contain fill for even distribution without leakage over time.
- Artisanal brands still producing domestically differentiate through heritage construction techniques and regional sustainable materials.
- Proper care like dry cleaning and low heat drying preserves the loft and longevity of your investment down comforter.
Understanding the intricacies of sourcing, cleaning, construction and materials demystifies exactly how these magical fluffy bedding essentials get made. Next time you dive under your down comforter, you’ll have warm and fuzzies knowing what went into creating such a quality cozy product.
Frequently Asked Questions
What’s the difference between white goose down and grey duck down?
In general, white goose down is considered superior with higher fill power and more resilience. Grey duck down comforters tend to be less expensive with slightly lower fill power around 600 compared to premium goose down in 700-900 range. However, both provide excellent insulation.
What fill power is the warmest down comforter?
For maximum warmth, you’ll want a comforter with fill power of 700 or higher. This ultra-high quality down contains more fluffy filaments and finer clusters filling more air pockets for unbeatable heat retention. Brands like Cuddledown use premium Hungarian goose down with 700-900 fill for outstanding insulation.
How much does a quality down comforter cost?
Expect to invest $200 – $500 for a luxury down comforter with ethically sourced materials, baffle box construction, and a high thread count cotton shell. Premium artisanal brands handcrafted domestically like Cuddledown or Plumeria Bay tend to fall on the higher end while imported mass-produced options run cheaper.
What’s the benefit of baffle box construction?
Baffle boxes created by intricate stitching patterns keep down fill evenly distributed so you enjoy consistent cozy warmth all night without cold spots as insulation shifts. This specialized sewing craftsmanship prevents the lightweight fill from clumping or moving.
How often should you replace a down comforter?
With proper care like dry cleaning and low heat drying cycles, a quality down comforter will last over a decade thanks to durable fabrics and resilient fill. If the outer shell shows signs of tearing or fill clumping, ask manufacturers about re-covering services to give your comforter new life by replacing the shell.